Glass Industry Machinery: The Backbone of Glass Production
The Glass Industry Machinery is without a doubt, a wide term. It includes every machine utilized to make glass items on a large scale. This is the machinery that performs every step of glassmaking. From the arrival of raw materials to the point where spun and molded glass products come out. Also known as channel benders, they are engineered to maximize productivity and correct glass processing speeds, as well as to maintain a consistent forging standard.
The Team Behind Glass Machine Manufacturing
Until specialized machinery was developed, glass could not have been produced in bulk. Try hand-making millions of glass bottles or panes of glass! Machinery utilized in the glass industry allows glass to be processed into the vast amounts needed in contemporary existence. These Glass Industry Machinery are not only about large quantities of glass; They’re also about creating glass of uniform quality and exact specifications. If you are looking for a top-notch, well-known Glass Industry Machinery Manufacturer then visit BAINENG CNC Equipment Co., Ltd.
Why is Glass Industry Machinery Important?
Enabling Mass Production
Glass industry machinery is primarily used to provide the prospect of mass production. Consider all the glass consumed in one city. Windows, car windshields, bottles, jars — you name it. Production therefore needs to be both massive and efficient to meet this demand. Glass-making machinery enables factories to manufacture great quantities of glass at speed and with great reliability.
Ensuring Consistent Quality
Glass products need quality to stay for longer periods. For things like safety glass in vehicles or precise lenses in eyeglasses, consistency is critical. The machinery in the glass industry is made in such a way that it can produce uniform and consistent glass in its thickness, transparency, and strength. Machinery with automatic processes and quality control standards built into it guarantees high standards.
Cut Down on Costs and Enhancing Safety
The upfront investment in glass machinery is high but lowers long-term costs. So we don’t need huge numbers of workers anymore, thanks to produced mechanized machines. In addition, it reduces material waste by exact operations. In addition, modern automated glass-developing machinery makes the glass-shaping process more secure. Automation also takes on the boring, dirty, and dangerous, freeing employees from unsafe environments.
Machinery Types in the Glass Industry
Handling Equipment for Raw Materials
The first step in the glassmaking process is gathering raw materials. These consist of sand, soda ash, limestone, and other components. This equipment is used to handle raw materials, including their movement, storage, and preparation. This can include:
· Conveyor Belts
These transport big volumes of raw products within the factory.
· Silos and Bins
Used for storing raw materials in a controlled state; keeping them dry and ready for utilization.
· Weighing and Batching Systems
These accurately measure and mix the correct proportions of the raw materials for each batch of glass.
Batching and Mixing Equipment
Batching and Mixing Equipment Raw materials, once measured, must be mixed thoroughly. They must be properly mixed, and batching and mixing equipment make sure that all ingredients throughout to make a well-incorporated melt.
· Mixers
Mixers mix through raw materials. Rotary mixers and screw mixers are commonly employed. Proper mixing produces a homogenous mixture of the glass material.
· Batch Chargers
Batch chargers do just that, feeding the mixed raw materials into the furnace. They regulate material throughput in the melting furnace. Charging for the furnace has to be controlled.
· Melting Furnaces
At the innermost core of glass making is melting. Melting furnaces take raw materials and raise them to extremely high temperatures. This turns them into molten glass.
· Regenerative Furnaces
Regenerative furnaces recover heat from exhaust gases and are known for their energy efficiency.
· Electric Furnaces
Most commonly used for specialty glasses or short runs, these allow for accurate temperature control.
· Day Tanks
Smaller melting systems for colored glass or small batches, bring flexibility in production.
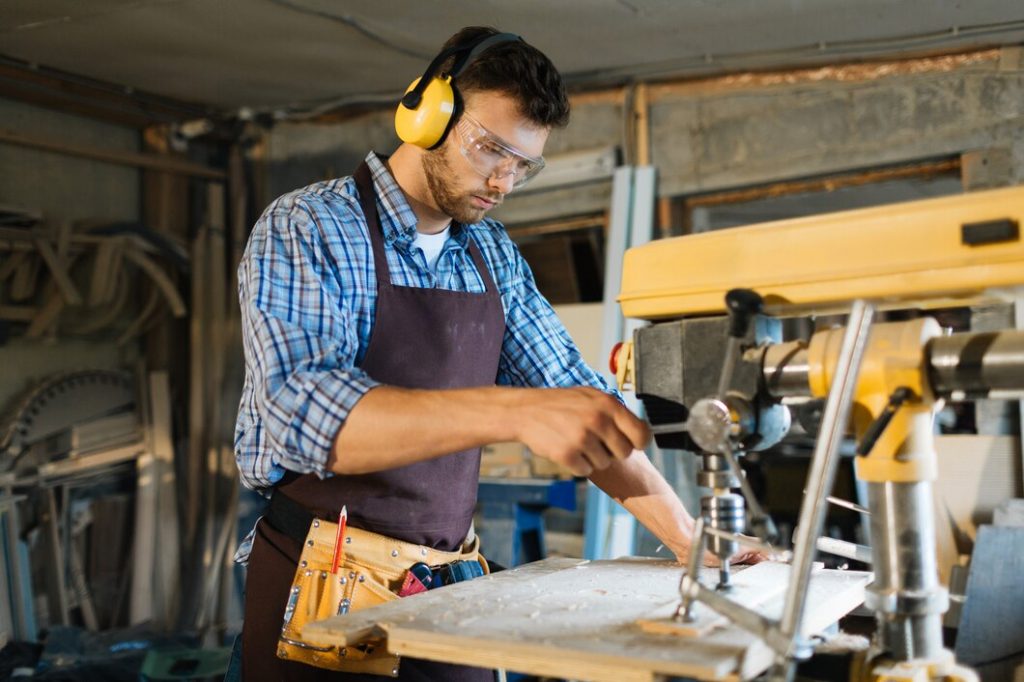
Forming Machines
You have to shape molten glass into products. Different glass shapes: Machines are used to produce glass shapes Various products require different techniques and machines:
· Float Glass Lines
These produce flat sheets of glass, typically to be used in windows or mirrors, by floating molten glass on a molten tin bed.
· Pressing Machines
Used to make containers and tableware pierce molten glass into molds to give the glass its shape
· Blowing Machines
Blow air into molten glass to shape, used for bottles and hollow glassware.
Annealing Lehrs
Once glass is formed, it is still hot and under mechanical stress. It must be cooled slowly, under control. This process is referred to as annealing. Annealing lehrs are long, heated tunnels where the glass cools slowly. It cools in a regulated manner, alleviating internal stresses that make it brittle and resulting in greater strength and durability.
Trimming and Separation Systems
Flat sheets or continuous strips of glass need to be cut to the desired size and shape. This is done with cutting and separation equipment. Computer-controlled cutters on automated cutting tables provide precision and speed. In the case of flat glass, scoring and breaking machines are used for straight cuts as well.
Quality Control Equipment
Throughout the glass manufacturing process, quality control plays a key role. Glass inspection machines are static or dynamic type equipment used for glass inspection. This includes:
· Online Inspection Systems
Automated systems that use cameras and sensors to automatically detect generation errors such as bubbles, scratches, or thickness differences in the course of production.
· Thickness Measurement Systems
Ensure that the glass thickness is within specifications using lasers or sensors.
· Defect Detection Systems
Detects different types of defects | optics-based / laser-based |
Processing and Finishing Equipment
Processing and Finishing Equipment Glassware needs to be further processed and finished after the basic forming and annealing. This category covers machines for:
· Grinding & Polishing Machines
Post Polish and Grinds — refine edges for safety and looks.
· Washing Machines
Weeding: Remove excess material from around the glass surface before coating, laminating, or other treatments.
· Coating Lines
These lines apply special coatings on the glass for color, reflectivity, or insulation properties.
Conclusion
Modern glass production stands on the pillars of the Glass Industry Machinery. It allows for the mass production of high-quality glass products that we all need in our daily lives. For glass companies to succeed, they must select the appropriate equipment, and stay informed on industry developments. The evolution of automation will bring new advancements to glass machinery, improving productivity and paving the approach for future glass production processes. Knowing about glass manufacturing equipment is essential for anyone involved in the glass business in order to remain competitive in the market.