Glass Manufacturing Equipment: An Overview
All the machines that are used to make glass are collectively included in Glass Manufacturing Equipment. This machinery operates at each stage throughout the process. It begins with raw materials and concludes with finished glass. These machines are ideal for mass production. They are fast and ensure consistent quality of glass.
Equipment for Glass Manufacturing in the Glass Sector
It enables the mass production of glass. This Glass Manufacturing Equipment is essential to produce enough glass for our requirements. This machinery helps make various shapes of glass.
The Scope of Manufacturing Equipment
Manufacturing equipment is vital for any type of glass. It has also made glass production safer and less expensive.
Glass Manufacturing Equipment Types
The process of glass making is a complex one. It involves many stages. Each of those stages requires some dedicated machines. Equipment suppliers provide a range of equipment for each stage of the process.
Handling Equipment for Raw Materials
Starting with raw materials. Sand, soda ash, and limestone are examples of raw materials for glass. Raw material handling equipment transports and readies these materials. This equipment can include:
· Conveyor Systems
Raw materials are transported around the plant by conveyor belts. They carry materials from storage to processing locations. Conveyors are particularly useful for transferring large quantities of materials.
· Silos and Storage Bins
Raw materials are stored in silos and bins until ready to be used. They keep materials dry and organized. These flour types are used as an ingredient, while proper storage ensures a continuous supply for production.
· Weighing and Batching Systems
Your data has to be right, everything depends on it, and this is particularly true for glass quality. Those that measure and mix raw materials are called weighing and batching systems. These systems ensure each batch of glass has the right mixture.
Batching and Mixing Equipment
Once the raw materials are proportioned, they need to be blended. The ingredients are mixed in the batching and mixing equipment. To make a well-incorporated melt.
· Mixers
Mixers mix through raw materials. Rotary mixers and screw mixers are commonly employed. Proper mixing produces a homogenous mixture of the glass material.
· Batch Chargers
Batch chargers do just that, feeding the mixed raw materials into the furnace. They regulate material throughput in the melting furnace. Charging for the furnace has to be controlled.
· Melting Furnaces
At the innermost core of glass making is melting. Melting furnaces take raw materials and raise them to extremely high temperatures. This turns them into molten glass.
· Regenerative Furnaces
In industrial glass manufacture, regenerative furnaces are a common technology. These devices recover heat from exhaust gases to preheat incoming air. It improves the energy efficiency of the energy exchanges.
· Electric Furnaces
Electric furnaces, as the name suggests, use electricity to melt the glass. They are commonly employed for specialized spectacles and lower batch sizes. Electric furnaces provide the ability to control temperature.
· Day Tanks
Day tanks are smaller melt units. For colored glass or small batches; there are not many. Production flexibility from gas Day tanks.
· Forming Machines
You have to shape molten glass into products. The glass is formed into its final shape by forming machines. Specific forming techniques are used on different glass products.
· Float Glass Lines
Floating glass lines are used to manufacture flat glass sheets. (True, they pour molten glass onto a molten tin bath.) This produces perfectly flat glass for windows and mirrors.
· Pressing Machines
These machines create glass by pushing liquid glass into cavities. It is used for producing glass containers and tableware. Pressing is a quick way to crank out large quantities of the same parts.
· Blowing Machines
Blowing machines use pressurized air to shape hot glass. This is then used to make bottles and hollow glassware. Complex forms can be created by blowing.
· Annealing Lehrs
Once glass is formed, it must be cooled slowly. It’s called annealing, and what this process does is… Annealing lehrs are long, heated tunnels that modulate cooling.
· Annealing Ovens
Annealing ovens gradually cool glass to minimize interior stress. This reduces cracking and improves the strength of glass. Glass durability depends on annealing, a key factor in the process.
· Cooling Zones
Annealing lehrs have cooling zones that are controlled. These zones progressively cool down the hot glass. Gradual cooling prevents thermal shock.
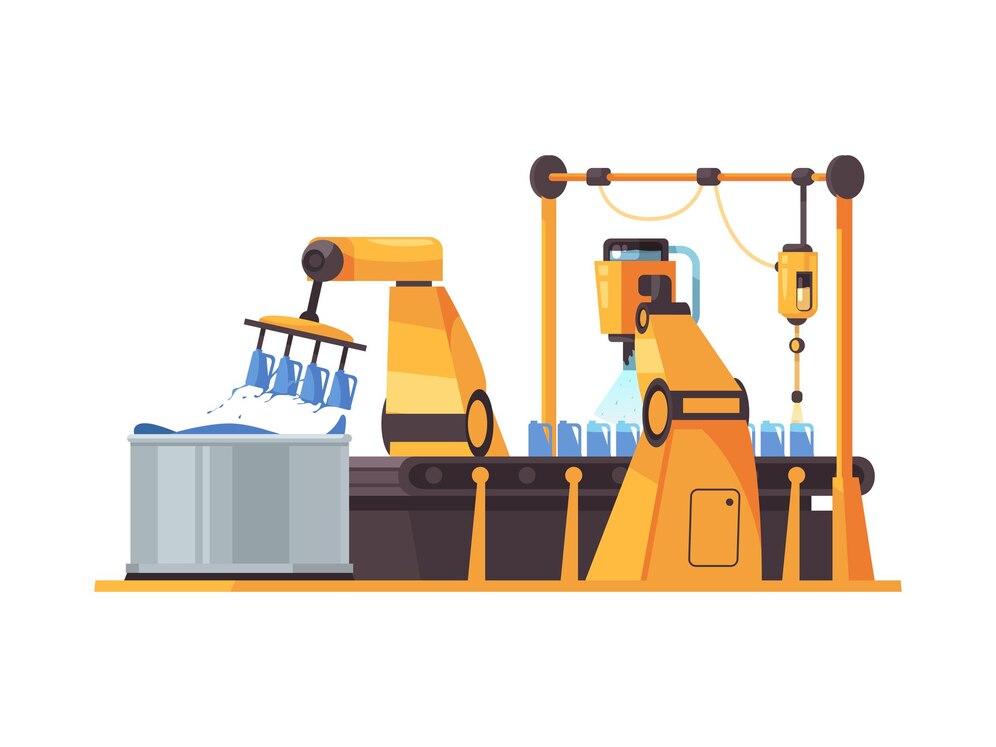
Cutting and Separation Equipment
Now, it is time to slice and divide the apparatus. They will need to be cut from continuous ribbons or sheets of glass. This includes cutting and separation equipment to cut the glass into the desired sizes and shapes.
· Automated Cutting Tables
Cutters that are computer-controlled are known as automated cutter tables. They cut glass sheets into given sizes as required. Automation raises speed and precision while cutting.
· Glass Scoring and Breaking Machines
Score and breaking machines score a line on the glass. Next, they use a controlled force to break the glass at the score. It is a standard way of cutting plate glass.
Quality Control Equipment
The quality of the glass is extremely important. Quality control equipment checks glass at different stages. This equipment is used to get the defects and also to check whether the standards are satisfied.
· Online Inspection Systems
Systems are available that automatically inspect the glass on velvet during production. Cameras and sensors are used to identify imperfections. Increased consistency of quality with automated inspection
· Thickness Measurement Systems
Thickness measurement systems ensure proper nag glass thickness. To measure the thickness of the glass, they use lasers or sensors. Ultimate performance and safety demand the correct thickness.
· Defect Detection Systems
A defect detection system detects the defects such as bubbles, scratches, and inclusions. These are optical and laser-based systems. Detecting defects early helps reduce waste.
Processing and Finishing Equipment
And glass needs post-processing after forming and annealing. Final touches with processing and finishing equipment
· Grinding & Polishing Machines
Grinding machines are used to smooth the edges of the glass. Glass surfaces are refined by polishing machines. These devices enhance looks and security.
· Washing Machines
Washing machines wash glass before coating or lamination.
· Coating Lines
Special coatings are applied to glass in coating lines. The coatings can provide beautiful color, optical reflectivity, or even thermal insulation. Coating controls functionality of glass.
What to Look for When Selecting Glass Manufacturing Equipment?
Selecting the appropriate gear is an important choice. It can impact production efficiency and glass quality. Important factors to consider when deciding to sign a record deal include:
· Production Volume and Scale
Larger operations will likely require larger equipment, but smaller operations may require more flexible equipment. Build capacity for whatever output you are looking to achieve.
· Types of Glass Products
Think about which type of glass your factory is going to produce.
· Degree of Automation and Technology
More automation means less manual work and greater output. Assess how automated you need to be.
Conclusion: Manufacturer Reputation and Support of Suppliers
Work with reliable equipment Manufacturers and Suppliers. Because trustworthy manufacturers and suppliers provide machines of high quality and reliable service. Think about after-sales support, availability of spare parts, and technical assistance. Visit BAINENG CNC Equipment Co., Ltd. If you want to buy cost-effective highly efficient Glass Beveling Machines.